A slightly delayed blog post this one, as it relates to developements back in early December: the installation of a new till system. While the setup is a bit nicer for customers, the real change has been felt by the staff. Here’s our longest serving co-op member, Chris, with a physical manifestiation of the bad data we were working with:
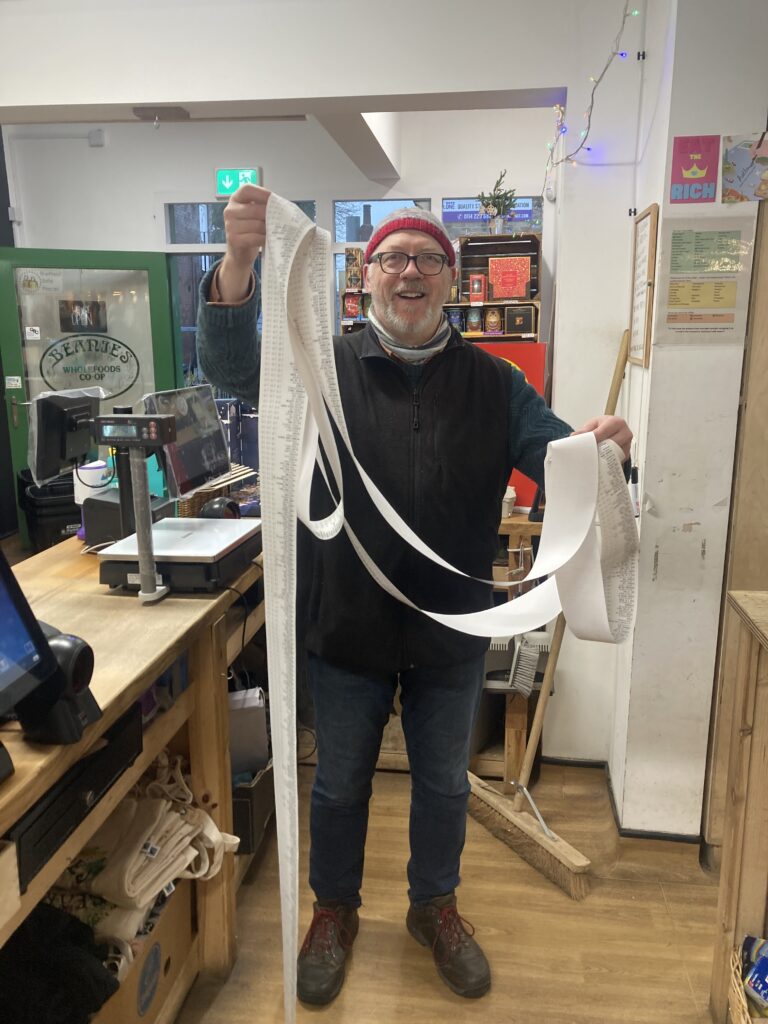
Up until late October the only way for us to get a full stocklist was to print it off the tills – that, or create a set of queries for a database that ran on software from 2002 (Access, if you need to know!). Chris is holding about 6 metres of till roll here and that’s just the non-organic fruit and veg. We could probably wrap the shop, Christo and Jeanne-Claude style, if we printed everything.
It sounds loopy when you put it like that, but as a bricks and mortar retail business we’re not unusual. Big technical upgrades are a huge investment in proportion to our actual size. Imagine T*sco doing this – it’s effectively the same project, but with an economy of scale far, far greater. Still it’s necessary, and this is the last big win in a five year project to take Beanies from the little shop down the road to a thriving, futureproof and stable business run on radical terms. I’d also like to mention that this project was partially funded by the UK Government through the UK Shared Prosperity Fund, and that the support we received from the team at Barnsley Council in putting our bid through was exceptionally helpful.
The new setup has brought us reliable stock control, ordering and reporting, freeing up staff time for the parts of our work that can’t, or shouldn’t, be automated. Supermarket systems are designed to edit out every possible human action, but we’re very careful about what we do and don’t try to digitise here, because you can’t put a barcode on a lettuce – you can only put a barcode on a plastic bag. So, rather than treat our staff as disposable, we train them to recognise and care for our veg.
Co-op members have the skills and autonomy to make decisions, not just perform tasks, and that means we don’t need best before dates or scannable packaging. And the reason we can afford to work in this way, investing in people and care, is because we’re not skimming off profits for shareholders or paying out massive executive salaries.
Obviously this is better for the environment because it results in less plastic in the system, and obviously it’s better for workers because they’re treated with respect. It’s also better for customers. Our produce is the best quality you’ll find in the city because it’s been looked after by people who know what they’re doing.
And for all the energy and commitment that goes in to running Beanies, we can still beat supermarkets on organic veg prices – because there is a better way to do things.
Ella